Plastic extrusion for strong and easy-to-handle components
Plastic extrusion for strong and easy-to-handle components
Blog Article
A Comprehensive Guide to the Refine and Advantages of Plastic Extrusion
In the huge realm of manufacturing, plastic extrusion emerges as a important and extremely effective process. Transmuting raw plastic right into continuous accounts, it deals with a variety of industries with its remarkable versatility. This overview intends to illuminate the intricate actions associated with this approach, the sorts of plastic apt for extrusion, and the game-changing advantages it gives the sector. The ensuing discussion assures to unravel the real-world impacts of this transformative process.
Understanding the Fundamentals of Plastic Extrusion
While it might show up complex at initial glimpse, the process of plastic extrusion is basically straightforward - plastic extrusion. It is a high-volume manufacturing method in which raw plastic is thawed and shaped into a constant account. The process begins with the feeding of plastic product, in the kind of granules, powders, or pellets, into a heated barrel. The plastic is after that thawed using a mix of warmth and shear, used by a rotating screw. When the molten plastic reaches the end of the barrel, it is forced via a tiny opening referred to as a die, forming it right into a preferred type. The shaped plastic is then cooled down, strengthened, and reduced right into preferred lengths, completing the process.
The Technical Refine of Plastic Extrusion Explained

Kinds of Plastic Suitable for Extrusion
The choice of the right type of plastic is an important facet of the extrusion process. Various plastics provide unique residential or commercial properties, making them a lot more suited to specific applications. Polyethylene, for example, is commonly utilized as a result of its affordable and very easy formability. It offers outstanding resistance to chemicals and wetness, making it excellent for products like tubes and containers. In a similar way, polypropylene is another preferred selection due to its high melting factor and resistance to fatigue. For even more durable applications, polystyrene and PVC (polyvinyl chloride) are typically picked for their toughness and toughness. Although these prevail options, the option inevitably depends on the specific demands of the product being produced. So, recognizing these plastic kinds can dramatically improve the extrusion procedure.
Comparing Plastic Extrusion to Various Other Plastic Forming Methods
Comprehending the kinds of plastic ideal for extrusion leads the way for a broader discussion on how plastic extrusion piles up versus various other plastic creating approaches. Plastic extrusion is exceptional when it comes to developing continuous profiles, such as pipes, seals, and gaskets. It additionally allows for a consistent cross-section along the length of the item.
Key Advantages of Plastic Extrusion in Manufacturing
In the world of production, plastic extrusion uses numerous significant advantages. One noteworthy benefit is the cost-effectiveness of the procedure, that makes it a financially appealing production approach. In addition, this method gives premium item versatility and improved manufacturing rate, thereby enhancing total manufacturing effectiveness.
Affordable Production Method
Plastic extrusion jumps to the leading edge as a cost-efficient manufacturing method in manufacturing. This procedure stands apart for its capability to produce high quantities of material quickly and successfully, supplying producers with considerable financial savings. The key price benefit is the ability to utilize cheaper resources. Extrusion utilizes polycarbonate products, which are less expensive contrasted to metals or porcelains. Additionally, the extrusion procedure itself is relatively straightforward, lowering labor expenses. Additionally, plastic extrusion needs much less energy than typical manufacturing approaches, find more adding to reduced operational prices. The process likewise minimizes waste, as any kind of faulty or excess materials can be recycled and recycled, supplying another layer of cost-effectiveness. In general, the economic advantages make plastic extrusion an extremely attractive choice in the manufacturing market.
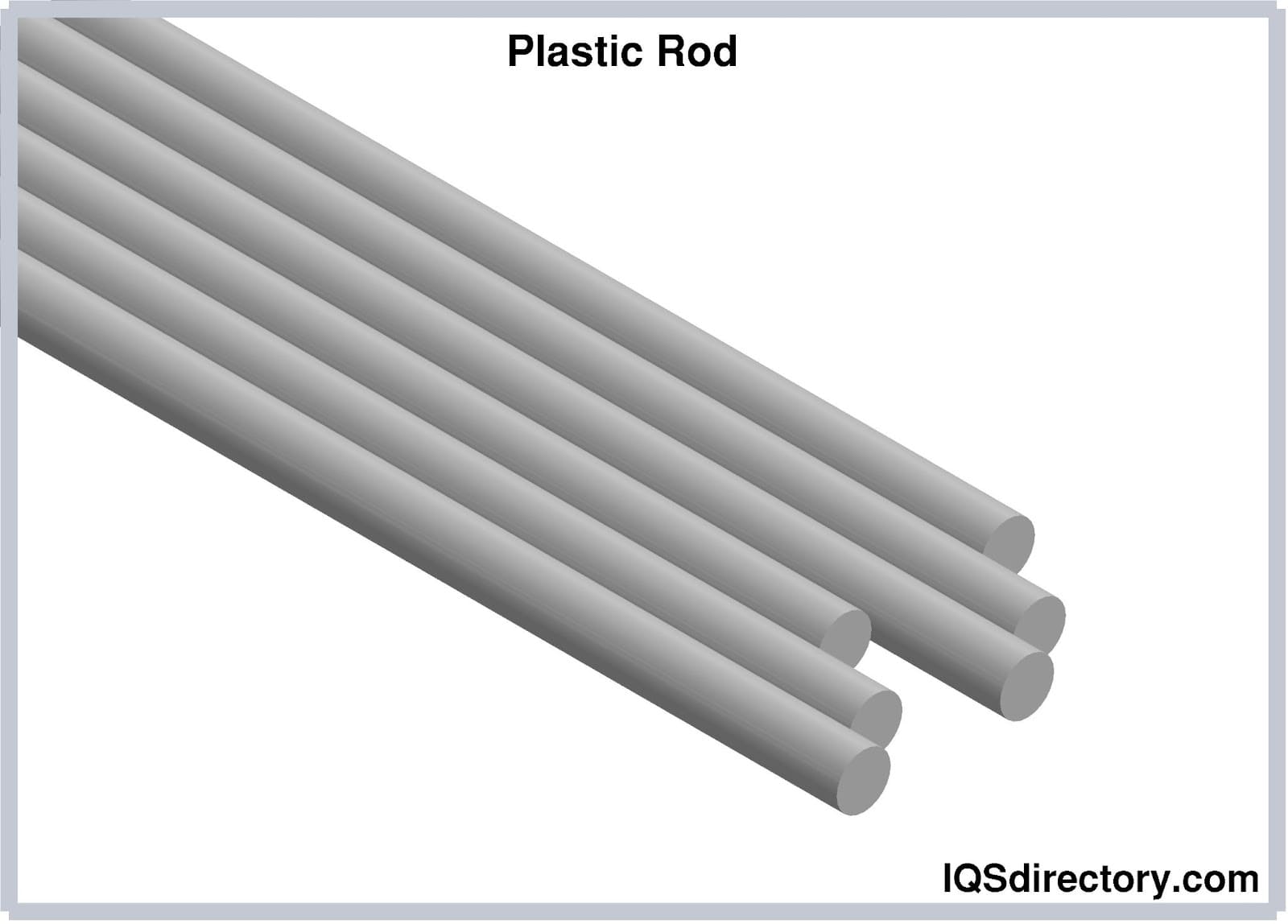
Superior Item Flexibility
Beyond the cost-effectiveness of plastic extrusion, an additional significant advantage in making lies in its exceptional product versatility. This makes plastic extrusion a suitable remedy for industries that need tailored plastic components, such as automobile, building, and packaging. In significance, plastic extrusion's product adaptability cultivates innovation while boosting functional performance.
Improved Manufacturing Rate
A significant benefit of plastic extrusion lies in its improved manufacturing speed. This production procedure allows for high-volume production in a reasonably short time span. It is qualified of generating long, continual plastic accounts, which significantly lowers the manufacturing time. This high-speed manufacturing is especially helpful in sectors where big amounts of plastic components are required within limited deadlines. Few other manufacturing processes can match the speed of plastic extrusion. In addition, the capacity to keep regular high-speed manufacturing without compromising product quality establishes plastic extrusion in addition to various other techniques. The improved production speed, for that reason, not only enables makers to satisfy high-demand orders but also adds to increased efficiency and cost-effectiveness. This useful attribute of plastic extrusion has actually made it a favored option in numerous industries.
Real-world Applications and Effects of Plastic Extrusion
In the realm of production, the method of plastic extrusion holds extensive value. This procedure is widely made use of in the production of a selection of products, such as plastic tubes, home window structures, and weather removing. Therefore, it considerably influences fields like building, packaging, and auto markets. Furthermore, its influence prolongs to daily items, from plastic bags to tooth brushes and non reusable cutlery. The economic benefit of plastic extrusion, primarily its economical and high-volume outcome, has actually reinvented production. However, the ecological influence of plastic waste stays an issue. Therefore, the market is persistently pursuing advancements in recyclable and naturally degradable products, indicating a future where the benefits of plastic extrusion can be preserved without compromising environmental sustainability.
Final thought
In final thought, plastic extrusion is a extremely effective and efficient method of transforming raw materials right into varied products. It provides various advantages over other plastic creating approaches, consisting of cost-effectiveness, high outcome, minimal waste, and design flexibility. Its impact view is profoundly felt in various markets such as building and construction, automotive, and durable goods, making it a pivotal procedure in today's production landscape.
Diving much deeper into the technical procedure of plastic extrusion, it begins with the choice of the ideal plastic material. As soon as cooled, the plastic is reduced into the called for lengths or wound onto reels if the product is a plastic movie or sheet - plastic extrusion. Contrasting Plastic Extrusion to Various Other Plastic Forming Methods
Recognizing the kinds of plastic appropriate for extrusion leads the means for a more comprehensive discussion on exactly how plastic extrusion piles up against various other plastic forming techniques. Couple of other like this production procedures can match the speed of plastic extrusion.
Report this page